CNC lathe machining, powered by Computer Numerical Control (CNC), has brought about a revolutionary shift in the realm of manufacturing, transforming the ways components and assemblies are produced.
This comprehensive article delves into the world of CNC lathe machining (CNCLM), starting from its historical origins to its widespread application in modern industries.
Thanks to the utilization of computerized control, CNCLM has led to remarkable advancements in accuracy, productivity, and the overall quality of production processes. As we delve into the intricacies, we will unravel the fundamental principles, benefits, and potential challenges associated with this cutting-edge technology.
Historical Development of CNC Lathe Machining
The historical development of CNCLM (or CNC turning) can be traced back to the mid-20th century when initial attempts were made to automate the functions of machines. During this period, the concept of numerical control programming emerged, and in the 1940s, the foundation for numerical control was laid with the invention of punched card systems in the laboratory of servo-mechanisms at the Massachusetts Institute of Technology.
Tracing the Origins of CNC Lathe Machining
The early origins of CNCLM can be dated back to the beginning of the 19th century when various endeavors were made to automate and mechanize the operations of lathes. Although the concept of numerical control programming, as we know it today, was not fully realized during this period, the seeds of automation were sown:
- One of the earliest developments that laid the groundwork for LM was the application of cam automation. Camshafts and mechanical cams were utilized to control the movements of the machine components, enabling repetitive operations. This basic form of automation increased productivity and process consistency;
- The industrial revolution at the end of the 18th and the beginning of the 19th centuries also played a significant role in advancing manufacturing technologies. Innovations in machine tools, such as lathes and milling machines, allowed for improved precision and efficiency in metalworking. However, early machines still required considerable manual intervention, limiting their automation capabilities;
- In the mid-19th century, the emergence of interchangeable parts and the concept of the assembly line further contributed to the development of production automation. American inventor Eli Whitney is often credited with popularizing the idea of interchangeable parts, which facilitated mass production and standardization of manufacturing processes;
- At the beginning of the 20th century, electric motors and electric control systems were introduced in lathes, leading to enhanced precision and controllability of movements. This progress was a crucial step toward numerical control programming;
- The true breakthrough in numerical control programming and the initial stages of CNCLM began in the 1940s. During World War II, American military forces sought ways to automate the production of complex parts for weaponry. As a result, the first computer-controlled lathe, based on punched card systems, was developed at the servo-mechanisms laboratory of the Massachusetts Institute of Technology. This innovation laid the groundwork for the concept of numerical control programming, which later evolved into Computer Numerical Control (CNC);
- The development of digital computers in the post-war era and subsequent advancements in electronics and computer technologies further accelerated the progress of CNCLM. By the 1950s, researchers and engineers began exploring the possibilities of using computers for full automation of machining operations.
The emergence of CNCLM can be attributed to the gradual evolution of automation, mechanization, and the early use of computer technologies in manufacturing processes. These initial developments paved the way for the sophisticated CNC lathe machines we operate today, driving enhanced accuracy, efficiency, and productivity across various industrial sectors.
Advancements in Electronics
The evolution and widespread adoption of CNCLM owe much to the pivotal role played by advancements in electronics. Over the years, developments in electronic components and technologies have continuously expanded the capabilities and productivity of CNC systems, making them more powerful, precise, and versatile.
Among the primary achievements in electronics that have influenced the development of CNCLM are:
- Transition from Vacuum Tubes to Transistors: In the early stages of electronics, vacuum tubes were used for amplification and switching. However, vacuum tubes were bulky, generated considerable heat, and were prone to failure. The invention of transistors in the late 1940s revolutionized electronics. Transistors became smaller, more reliable, and consumed less power, enabling the creation of more compact and efficient CNC control systems;
- Integrated Circuits (ICs): The development of integrated circuits in the 1960s further revolutionized electronics. ICs allowed multiple electronic components to be integrated on a single chip, reducing the size of electronic systems and enhancing their reliability. The use of integrated circuits in CNC control units increased the efficiency and cost-effectiveness of the machines;
- Microprocessors and Microcontrollers: The advent of microprocessors and microcontrollers in the 1970s and 1980s marked a significant milestone in the development of CNCLM. These small yet powerful computing devices enabled CNC systems to execute more complex instructions and perform intricate calculations, expanding the capabilities of turning and programming;
- Digital Servo Systems: Breakthroughs in digital signal processing and servo motor technology revolutionized motion control in CNC lathes. Digital servo systems provide higher accuracy, rapid responsiveness, and smoother motion, resulting in improved surface finishes and enhanced part quality;
- Software and CNC Programming: As electronics advanced, so did the software used in CNC lathes. The development of Computer-Aided Design (CAD) and Computer-Aided Manufacturing (CAM) software allowed for optimized design and programming processes. Enhanced programming languages, such as G-code and high-level programming languages, enabled the creation of more complex and sophisticated tool paths;
- Human-Machine Interfaces (HMI): The development of user-friendly interfaces made CNC lathes more accessible to operators with varying skill levels. Touchscreen interfaces, visualization, and graphical programming simplified machine control and reduced training time for new users;
- Networking Technologies and Connectivity: Modern CNC lathes are often equipped with networking capabilities, enabling integration into larger manufacturing systems. Network communication facilitates data exchange, remote monitoring, and centralized control, enhancing productivity and efficiency;
- Sensors and Feedback Systems: Advancements in sensor technologies have enabled real-time feedback and monitoring of processes. Encoders, laser measurement systems, and other sensors provide precise information on tool position, workpiece dimensions, and cutting conditions, enabling adaptive control and error correction.
The continuous progress in electronics has revolutionized CNCLM, making it an indispensable technology in modern production. These achievements have led to increased productivity, accuracy, reduced downtime, and improved safety, contributing to the growth and competitiveness of industries worldwide.
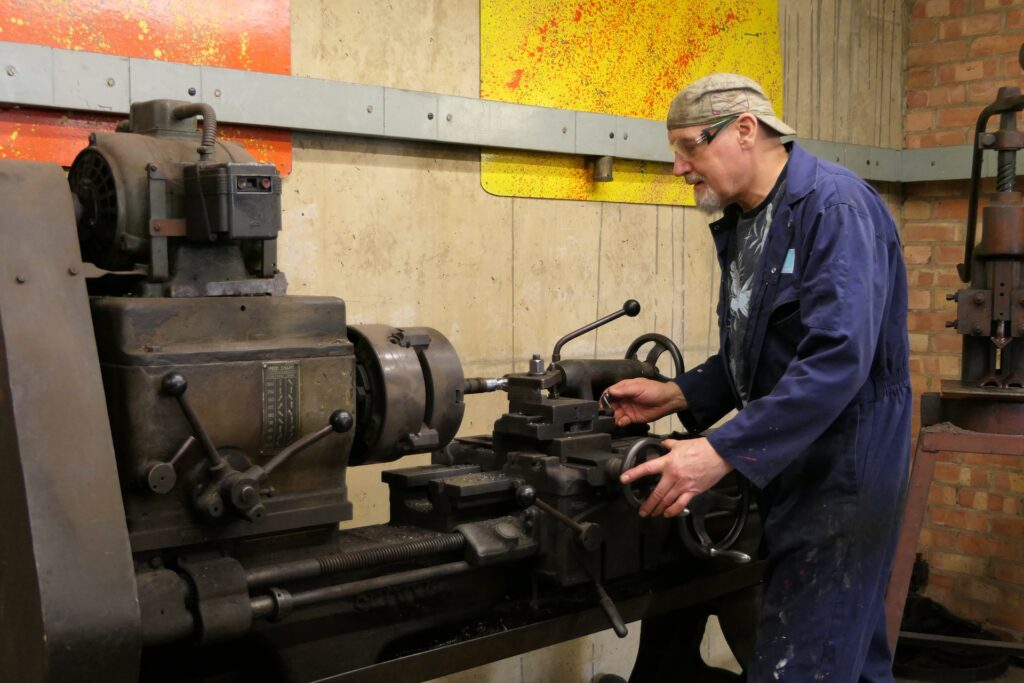
Types of CNC Lathes
CNC lathes come in various configurations and designs, each tailored to specific processing requirements and tasks. The types of CNC lathes can be classified based on their construction, size, and functional capabilities. Below are some common types of CNC lathes:
- 2-Axis CNC Lathes: Also known as “2-axis CNC turning centers,” these lathes have two axes of movement, typically the X-axis and Z-axis. They are mainly used for simple turning operations, where the cutting tool moves in a straight line along the outer diameter of the workpiece. 2-axis CNC lathes are commonly found in workshops and small-scale production;
- Multi-Axis CNC Lathes: Multi-axis CNC lathes have more than two axes of movement, providing greater flexibility and the ability to perform complex operations. Typically, 3, 4, and 5-axis CNC lathes are used, with additional axes enabling simultaneous machining in multiple directions. These lathes are ideal for manufacturing parts with intricate shapes and contours;
- Swiss-Type CNC Lathes: Swiss-type CNC lathes, also known as Swiss-type lathes or sliding headstock lathes, are designed for high-precision turning of small-diameter parts. They feature a guide bushing that supports the workpiece in close proximity to the cutting tool, ensuring enhanced rigidity and accuracy. Swiss-type CNC lathes are widely used in industries such as medical, electronics, and watchmaking;
- CNC Turning Centers: CNC turning centers are versatile machines that combine the capabilities of a CNC lathe with additional functions like milling, drilling, and thread cutting. These machines have live tooling, allowing them to perform both turning and milling operations in a single setup. CNC turning centers are widely used for producing complex parts with reduced setup times;
- Vertical CNC Lathes: Vertical CNC lathes have a vertical orientation, with the workpiece mounted on a rotating table that moves vertically along the Z-axis. The cutting tool is fixed in a horizontal position, enabling stable machining of large and heavy workpieces. Vertical CNC lathes are prevalent in industries such as aerospace and automotive, where large-diameter parts are produced;
- Horizontal CNC Lathes: Horizontal CNC lathes have a horizontal orientation, with the workpiece mounted on a rotating spindle that moves horizontally along the Z-axis. These lathes are suitable for various turning operations and are commonly used in mass production. They find extensive use in industries such as automotive, oil and gas, and general manufacturing;
- Slant Bed CNC Lathes: Slant bed CNC lathes have an inclined bed, which provides better chip evacuation and improved tool access to the workpiece. This design offers increased rigidity, making it suitable for heavy cutting and high-speed performance. Slant bed CNC lathes are commonly used in industries that require high precision, such as aerospace and medical;
- Flat Bed CNC Lathes: Flat bed CNC lathes have a horizontal bed that provides stability and rigidity during turning. They are designed for turning heavy-duty parts, such as large-diameter shafts and components. Flatbed CNC lathes are widely used in industries such as oil and gas, construction equipment manufacturing, and power generation;
- Manual and CNC Combination Lathes: Manual and CNC combination lathes, also known as manual/CNC lathes, are hybrids that allow operators to manually control the tool movement while recording the sequence of actions as a CNC program. These lathes are convenient for prototyping and small-batch production.
Each type of CNC lathe offers unique advantages and is best suited to address specific machining tasks. Manufacturers and machinists can choose the appropriate CNC lathe based on their production requirements, desired level of automation, and the complexity of the parts they need to manufacture.
Understanding CNC Lathe Machining
CNCLM is a sophisticated manufacturing process that utilizes computer-controlled machines to precisely shape and cut materials into intricate components and parts. This technology has become the cornerstone of modern production due to its unparalleled accuracy, efficiency, and repeatability.
Understanding the fundamental principles and components of CNCLM is essential for realizing its significance and application in various industries.
The Basics of CNC Lathe Machining
CNCML is a subtractive manufacturing process where the material is removed from the workpiece using rotating cutting tools to achieve the desired shape and size. Unlike traditional manual lathes, CNC lathes are fully automated and controlled by pre-programmed computer instructions.
The CNC system reads the program code and controls the movement of the machine components, including the cutting tool and workpiece. The program code, often written in G-code or other programming languages, defines the precise toolpath, cutting speed, and depth, enabling complex and accurate machining operations.
Components of a CNC Lathe Machine
A typical CNC lathe machine consists of several main components that work together to perform the turning process:
Component | Description |
---|---|
Bed | Foundation of the machine; provides stability and support |
Headstock | Houses the spindle that rotates the workpiece |
Chuck | Clamping device mounted on the spindle to hold the workpiece |
Tailstock | Provides additional support for long workpieces |
Tool Turret | Holds multiple cutting tools; can rotate and index automatically |
Control Panel | Interface for the operator to interact with the CNC machine |
Axis Drive Systems | Drives and controls the movement of machine axes |
Coolant System | Dispenses coolant to dissipate heat and wash away chips |
CNC Controller | The computerized system that interprets and executes CNC programs |
Servo Motors | Drives and controls the movements of the machine components |
Encoders | Provides feedback on position and movement for precise control |
Ball Screws/Linear Guideways | Translates rotary motion to linear motion for axes movement |
Spindle Drive | Powers and controls the rotation of the spindle |
Safety Enclosure | Protects operators from rotating parts and flying chips |
Working together, these components allow the CNC lathe machine to perform precise and automated operations.
Programming CNC Lathe Machines
Programming CNC lathe machines is a crucial aspect of the manufacturing process as it determines how the machine will execute the required turning operations. CNC programming involves writing a set of instructions in a specific code, such as G-code or ISO code, that the CNC machine can understand and execute.
The programming process requires a good understanding of the machine’s capabilities, workpiece design, cutting tool, and required machining operations. The following are the main steps in programming CNC lathe machines:
- Understanding the Workpiece and Requirements: The first step in CNC programming is a thorough study of the workpiece’s design and dimensions. Analyze engineering drawings, 3D CAD models, or 2D blueprints to determine the required toolpaths and operations. Identify critical features, dimensions, and tolerances that must be maintained during the process;
- Selecting the Cutting Tools: Choose the appropriate cutting tools based on the material properties, workpiece geometry, and desired surface finish. Different cutting tools, such as turning, boring, threading, and grooving tools, are used for specific operations. Ensure that the selected tools are compatible with the CNC lathe’s tool turret or tool holders;
- Creating the CNC Program: CNC programs are typically written in G-code, a programming language consisting of a series of commands and coordinates. Computer-Aided Manufacturing (CAM) software is often used to automatically generate CNC programs based on 3D CAD models or 2D blueprints. Additionally, experienced programmers can write programs manually;
- Defining Parameters: For each operation, the cutting speed, feed rate, depth of cut, and other parameters need to be defined to optimize material removal and achieve the desired surface finish. Proper selection of parameters is critical for efficient and accurate results;
- Defining Toolpath and Tool Compensation: Determine the toolpath for each cutting operation. The toolpath defines the trajectory along which the cutting tool will move to remove material from the workpiece. Pay attention to tool movements, such as approach, engagement, and retraction, to avoid collisions and ensure safe processing;
- Coordinate System and Workpiece Offsets: Establish the machine’s coordinate system (work zero) based on reference points on the workpiece. Work offsets are used to set reference positions along the X, Z, and sometimes Y axes to let the CNC machine know where the workpiece is located in the work zone;
- Testing and Verifying the CNC Program: Before running the CNC program on the actual workpiece, it should be tested and verified using simulation or CNC machine simulator software. Simulation allows identifying potential errors, collisions, or issues in the program, preventing costly mistakes during the actual process;
- Loading and Running the CNC Program: After the CNC program has been tested and verified, it is loaded into the CNC lathe’s control system. Securely mount the workpiece in the chuck or between centers and ensure proper tool setup. Start the process by closely monitoring the initial toolpath to ensure correct engagement;
- Monitoring and Troubleshooting: During turning, the operator should monitor the process for any unexpected issues, tool wear, or material deviations. Adjust cutting parameters or tool offsets as needed to maintain quality and accuracy;
- Post Inspection: After completing the process on the CNC lathe, the finished part should be inspected using precision measuring instruments to ensure its dimensions and tolerances. Additional operations, such as deburring or surface finishing, may be required to meet specific requirements.
Effective programming of CNC lathe machines is essential for achieving quality and efficient results. Proper programming, combined with a comprehensive understanding of the CNC lathe’s capabilities, allows manufacturers to optimize productivity, reduce cycle times, and produce precision parts for various industries.
CNC Lathe Machining Process
CNCLM is a highly automated manufacturing method that uses computer-controlled machines to shape and cut materials into precise components and parts. This process has numerous advantages, such as increased accuracy, efficiency, and consistency, making it a cornerstone of modern production. Below is a step-by-step overview of the CNCLM process:
- Workpiece Setup: The first step in the CNCLM process is to set up the workpiece on the lathe machine. The workpiece is securely clamped in a chuck, holding it in place during the process. For longer workpieces, a tailstock may be used to support the other end;
- Tool Selection: Next, based on the processing requirements, material properties, and desired surface finish, the appropriate cutting tool is selected. Different types of cutting tools are used for specific operations, such as turning, milling, threading, and grooving;
- CNC Program Loading: A CNC program is loaded into the lathe machine, containing a set of instructions that define the operations. The CNC program is typically written in G-code, a programming language that the machine can understand and execute;
- Coordinate System and Work Offsets: Before starting the process, the operator sets the lathe machine’s coordinate system or work zero based on reference points on the workpiece. Work offsets are used to define reference positions along the X, Z, and sometimes Y axes, allowing the CNC machine to know the workpiece’s location.
Once the workpiece is set up, and the CNC program is loaded, the process can be initiated. The CNC lathe machine, following the programmed instructions, moves the cutting tool across the workpiece’s surface, removing material to create the desired shape and dimensions.
Advantages of CNC Lathe Machining
CNCLM offers several significant advantages over traditional manual methods:
Advantages of CNC Lathe Machining | Explanation |
---|---|
Precision and Accuracy | CNC lathe machines can achieve high levels of precision, ensuring consistent and repeatable results. |
Efficiency and Productivity | Automation and reduced setup times lead to faster production cycles and increased overall efficiency. |
Versatility | Such machines can work with various materials, including metals, plastics, and composites, making them suitable for diverse applications. |
Complex Shape Machining | These machines can produce intricate and complex shapes that would be challenging or impossible to achieve manually. |
Consistency | CNCLM ensures that each component produced is identical to the programmed specifications, minimizing variations. |
Reduced Human Error | Automation reduces the risk of human errors during the process, resulting in higher quality and reduced scrap rates. |
Enhanced Safety | CNC lathe machines are designed with safety features to prevent accidents, making the process safer for operators. |
High Material Removal Rates | CNC lathe machines can perform high-speed cutting, enabling faster material removal and reducing cycle times. |
Multi-Axis Machining | Multi-axis CNC lathes offer the ability to perform complex and simultaneous turning from multiple directions, reducing the need for multiple setups. |
Repetitive Manufacturing | CNCLM is ideal for high-volume production, where consistent quality is required for each part. |
Reduced Labor Costs | CNC lathe machines require fewer operators and can run unattended for extended periods, reducing labor costs. |
Quick Prototyping and Iterative Design Changes | CNC programming allows for quick changes in part design, enabling rapid prototyping and iterative improvements. |
Improved Surface Finish | CNC lathe machines can achieve excellent surface finishes, reducing the need for additional post-processing operations. |
CNCLM has numerous benefits that make it a vital technology in modern manufacturing processes. The precision, efficiency, and versatility of this technology have revolutionized industries, enabling the production of complex parts with consistent quality.
Applications of CNC Lathe Machining
CNCLM finds applications in various industrial sectors, including the following.
Applications of CNCLM | Explanation |
---|---|
Aerospace Components | CNCLM is widely used in aerospace to manufacture critical components like engine parts, landing gear elements, and structural components with high precision and quality. |
Automotive Parts | CNC lathe machines produce various automotive parts, including engine components, transmission parts, shafts, and axle components, ensuring accuracy and consistency. |
Medical Devices and Implants | CNCLM is utilized to create intricate medical device components, orthopedic implants, and surgical instruments, meeting stringent tolerances and surface finish requirements. |
Electronics and Consumer Electronics | CNC lathe machines manufacture electronic components, connectors, housings, and other parts used in consumer electronics and devices, ensuring precise dimensions and smooth finishes. |
Oil and Gas Machinery | In the oil and gas industry, CNCLM is applied to produce components used in drilling equipment, valves, pumps, and other critical machinery parts with high reliability and performance. |
Power Generation Equipment | CNCLM plays a vital role in producing components for power generation equipment like turbines, generators, and turbines, ensuring efficiency and durability. |
Renewable Energy Systems | CNCLM is used to manufacture components for renewable energy systems, such as wind turbine parts, solar panel frames, and hydroelectric equipment. |
General Manufacturing | CNC lathe machines are widely utilized in general manufacturing to create a vast range of components, parts, and products for various industries, enhancing productivity and quality. |
Defense and Military Equipment | CNCLM is employed to manufacture parts and components for defense and military equipment, ensuring precision and reliability in critical applications. |
Industrial Machinery and Equipment | CNC lathe machines are used to produce parts and components for industrial machinery, such as gears, bearings, and machine tool components. |
Construction Equipment | CNCLM is applied to create parts for construction equipment, including bulldozers, excavators, and cranes, ensuring robustness and accuracy. |
Marine and Shipbuilding Industry | CNCLM is utilized to produce components for ships and marine equipment, ensuring high quality and performance in demanding marine environments. |
These are just a few examples of the broad range of applications of CNCLM across different industries. The precision, efficiency, and versatility of CNC lathe machines have made them indispensable tools in modern production, facilitating the creation of intricate components and products worldwide.
Future Trends in CNC Lathe Machining
The field of CNCLM is constantly evolving, driven by technological advancements and industrial demands. In the coming years, the development and application of CNCLM are expected to be shaped by several promising trends.
Here are some key trends in the field:
- Automation and Smart Manufacturing: Automation will play a pivotal role in the future of CNCLM. Manufacturers will increasingly integrate robotics and automation technologies into CNC lathe machines, enhancing unmanned operation and lights-out production. Concepts of smart manufacturing, such as the Industrial Internet of Things (IIoT) and cyber-physical systems, will enable real-time data collection, analysis, and adaptive control, optimizing machining processes for improved efficiency and productivity;
- Integration of Artificial Intelligence (AI): AI will find its application in CNCLM, providing self-learning and predictive capabilities. Machine learning algorithms will analyze data from past operations to optimize cutting parameters, predict tool wear, and automatically adjust strategies to enhance accuracy and reduce downtime. Virtual simulation using AI will help optimize tool paths and reduce cycle times;
- Processing of Advanced Materials and Composites: As industries demand lightweight and high-performance materials, CNC lathe machines will adapt to process modern materials and composites. Developments in materials and cutting tool coatings will enable CNC lathes to efficiently process materials such as titanium alloys, carbon fiber-reinforced composites, and high-temperature alloys used in aerospace and other high-tech sectors;
- Hybrid Machining: Hybrid manufacturing, combining CNC machining and additive manufacturing (3D printing), is gaining popularity. CNC lathe machines with integrated 3D printing capabilities will produce complex parts with optimized material distribution, reducing waste and lead times. The hybrid type will open up new design possibilities and provide increased production flexibility;
- Improved Surface Accuracy and Quality: Advancements in CNC control systems, sensors, and servo technologies will lead to even higher levels of surface machining accuracy and quality in CNC lathe machines. Real-time feedback from sensors will enable adaptive control, compensating for temperature fluctuations, tool wear, and material properties to achieve tighter tolerances and improve surface quality;
- Energy Efficiency and Sustainable Development: Efforts to reduce energy consumption and promote sustainable manufacturing will influence the design and operation of CNC lathe machines. Energy-efficient drive systems, regenerative braking, and intelligent power management will be integrated into CNC lathe machines to increase environmental friendliness;
- Human-Machine Interaction: User-friendly human-machine interfaces (HMIs) and augmented reality (AR) will enhance operator convenience and simplify the programming and operation of CNC lathe machines. AR-assisted maintenance and remote troubleshooting will increase machine uptime and reduce downtime;
- High-Speed Machining and Additive-Subtractive Hybrid Processing: High-speed machining technologies will develop further, increasing material removal rates and reducing cycle times. Additionally, additive-subtractive hybrid turning, where 3D printing is combined with CNCLM, will offer cost-effective solutions for producing complex geometric shapes with high precision;
- Integration with Supply Chain and Digital Manufacturing: CNCLM will be integrated with digital manufacturing processes, enabling seamless data exchange and collaboration across the entire supply chain. Such integration will allow rapid design changes, quick prototyping, and on-demand production, increasing overall production flexibility;
- Nanotechnology in Cutting Tools: Nanotechnology will lead to the creation of cutting tools with nanoscale coatings and geometry, increasing the tool’s lifespan, wear resistance, and chip evacuation capabilities. These advanced cutting tools will enhance the productivity of processing various materials.
These promising directions in CNCLM reflect a continuous pursuit of innovation and optimization in manufacturing processes. As technology continues to evolve, CNC lathe machines will play a key role in solving industrial challenges and driving progress in various industries.
Conclusions
CNC lathe machining has undoubtedly revolutionized manufacturing, providing unprecedented accuracy, efficiency, and quality in various industries. Its historical evolution, fundamental principles, and diverse applications demonstrate its transformative potential.
Thanks to ongoing technological progress, CNCLM will play a leading role in future production, turning the world of automated precision into a reality.