High-precision manufacturing processes are the backbone of numerous industries today, with Computer Numerical Control (CNC) machining leading the way. Among the plethora of materials CNC machines can manipulate, aluminum stands out for its unique characteristics and benefits. This article delves into the world of aluminum CNC services, illuminating the intricacies and benefits involved, and answering frequently asked questions.
Aluminum: A Preferred Material in CNC Machining
When it comes to CNC machining, the choice of material plays a crucial role in determining the success of a project. Among the plethora of materials available, aluminum stands out as a preferred and versatile option, offering numerous benefits that make it an excellent choice for a wide range of applications. Let’s delve into the reasons why aluminum is often the top choice for CNC machining projects:
1. Lightweight Advantage
Aluminum is celebrated for its remarkable lightweight nature, weighing in at just one-third of the weight of steel. This unique characteristic makes it highly sought-after in industries such as aerospace and automotive, where reducing overall weight is of paramount importance. In these sectors, every ounce saved translates into enhanced fuel efficiency, increased payload capacity, and improved performance. Additionally, for parts that require ease of handling and transportation, aluminum’s lightweight advantage proves to be invaluable.
2. Strength and Durability
Despite its low density, aluminum exhibits impressive strength comparable to certain types of steel. This exceptional strength-to-weight ratio allows manufacturers to design and produce robust components that can withstand demanding conditions without compromising on performance. The inherent durability of aluminum also ensures the longevity of parts, making it a reliable choice for critical applications.
3. Corrosion-Resistant Properties
Aluminum boasts natural corrosion-resistant properties, thanks to its ability to form a thin, protective oxide layer on its surface when exposed to oxygen. This oxide layer acts as a shield, safeguarding the metal from environmental factors that could otherwise lead to corrosion and degradation. For enhanced protection, aluminum can undergo processes like anodization, which further fortify its resistance to corrosion, making it particularly suitable for outdoor and marine applications.
4. Excellent Thermal and Electrical Conductivity
Another compelling advantage of aluminum is its exceptional thermal and electrical conductivity. Compared to many other materials, aluminum is an outstanding conductor of heat and electricity. This attribute makes it a favored choice for electronic devices, heat sinks, and heat transfer applications. The efficient dissipation of heat ensures that sensitive components are safeguarded from overheating, optimizing the overall performance and reliability of the final product.
5. Malleability for Complex Designs
Aluminum’s remarkable malleability grants designers and engineers the freedom to create intricate and complex designs with ease. This characteristic opens up a plethora of possibilities in terms of part geometries and shapes, making it a popular choice for industries that require custom components tailored to specific needs. CNC machining can fully exploit aluminum’s malleability to produce parts with precision and accuracy, meeting even the most intricate design requirements.
The Process: A Deep Dive into Aluminum CNC Services
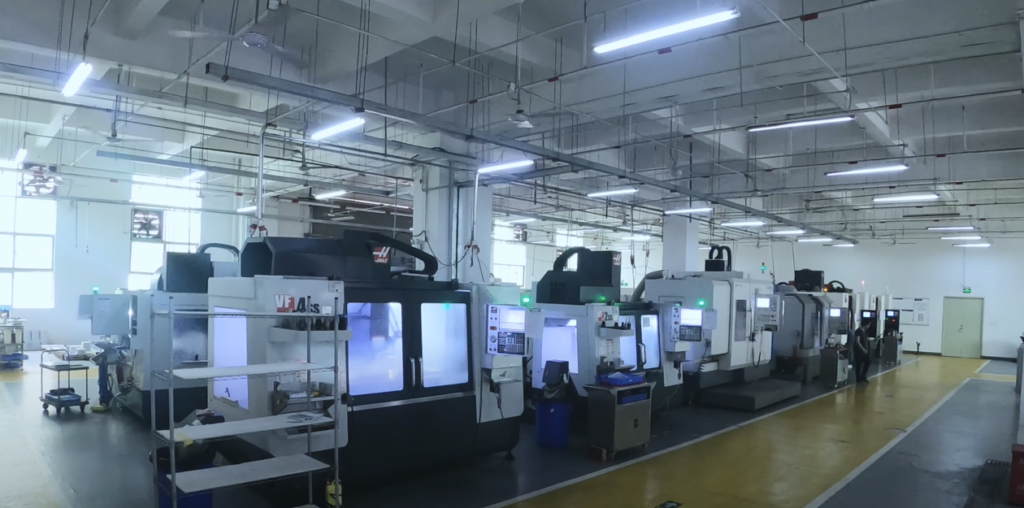
The value proposition of Aluminum CNC services lies in its ability to deliver high-quality, precisely machined components with consistency and efficiency. This becomes possible due to the five-phase procedure that these services follow.
CAD Model Design
- Step 1: Defining the Component: The process commences with defining the end product or component. This definition includes specifying the component’s size, shape, and features;
- Step 2: Developing the CAD Model: Next, a team of expert engineers develop a detailed CAD (Computer-Aided Design) model based on these specifications. This model serves as a digital blueprint for the final product.
Conversion to CNC Program
- Step 3: Conversion to CNC Language: The completed CAD model is then translated into a CNC (Computer Numerical Control) program. This program contains explicit instructions, often in G-code language, which control the movement of the CNC machine and its cutting tools;
- Step 4: Simulation and Validation: Prior to the machining process, the CNC program is simulated to validate the program’s integrity and to anticipate potential issues.
CNC Machining
- Step 5: Loading the Aluminum Block: An unshaped block of aluminum, the raw material for the part, is placed into the CNC machine;
- Step 6: CNC Machining: The CNC machine follows the program’s instructions, using an array of cutting tools to shape the aluminum block into the desired form. This process is often carried out with high precision, thanks to the advanced control systems of the CNC machine.
Post-Processing
- Step 7: Deburring: After machining, the product undergoes a process known as deburring, which removes any unwanted pieces of material left over from the machining process;
- Step 8: Cleaning and Surface Treatments: The product is then cleaned and may receive additional surface treatments such as anodizing, powder coating, or painting, to improve the part’s aesthetic appeal or functional characteristics.
Quality Assurance
- Step 9: Quality Inspection: Finally, the finished product is rigorously inspected for any defects or variations from the original design. Advanced metrology tools are often used for this purpose to ensure accurate measurements;
- Step 10: Approval and Delivery: If the product meets all quality standards, it is approved for delivery to the customer.
This five-step process is meticulously followed to ensure the accuracy, precision, and efficiency in the production of aluminum parts, thus revealing the true worth of Aluminum CNC services.
Industries Benefiting from Aluminum CNC Services
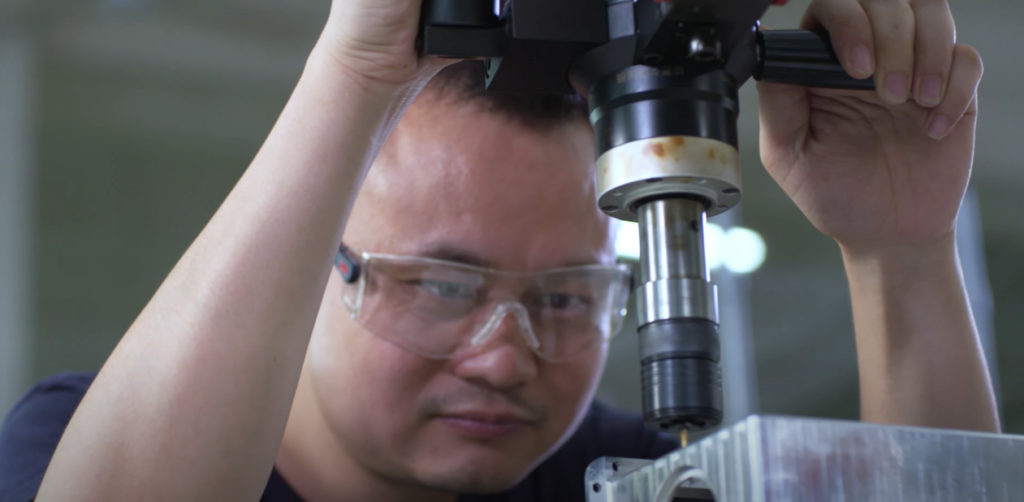
A diverse range of industries utilizes aluminum CNC services due to the aforementioned advantages. Some of these sectors include:
- Automotive and Aerospace: These industries use aluminum CNC services to manufacture lightweight and strong components such as engine parts, car bodies, and aircraft frames;
- Electronics: In this sector, CNC machines are used to produce heat sinks, casings, and other parts due to aluminum’s thermal conductivity;
- Medical Devices: Precision and reliability are paramount in the medical field. Hence, CNC services are employed to manufacture medical devices and surgical tools;
- Construction and Infrastructure: The durability and corrosion resistance of aluminum make it a preferred choice for many construction and infrastructure applications;
- Energy Sector: Aluminum CNC services are used to manufacture components for both traditional and renewable energy industries, including wind turbine parts, solar panel frames, and more.
Conclusion
The aluminum CNC service offers an advanced and flexible solution for manufacturing various parts and components. It provides unparalleled precision, efficiency, and versatility that serves a broad range of industries. With the continuous advancement of CNC technology, the capabilities and applications of aluminum CNC services will only continue to expand.
FAQ
Both CNC mills and lathes are used for aluminum. CNC mills are perfect for complex shapes and high precision, while CNC lathes are ideal for cylindrical parts.
Yes, CNC machining can accommodate both small and large parts depending on the size of the CNC machine used.
Precision is guaranteed through rigorous quality control processes, which include dimensional checks and surface inspections.
While the initial cost might seem high, the long-term benefits such as durability, precision, and reduced waste make it a cost-effective solution.