Over the past ten years, the worldwide industry has seen significant technical advancements that have fundamentally changed several areas of the manufacturing process. Grinding machines are one of the main areas where innovation has significantly changed the way materials are processed. With the newest technical breakthroughs, these devices have experienced a revolution and are essential to achieving excellent surface quality and precision. Let’s examine some of the most noteworthy advancements in this area of study.
Automation & intelligent technology
Combining AI with
Mechanical engineering’s most cutting-edge technical developments & materials processing can be found in today’s AI-integrated grinding apparatus. The aforementioned machines use AI & apparatus learning techniques to evaluate and adjust their operational settings based on real-time data obtained from the grinding process. There are some important factors that need to be considered before implementing AI in grinding devices.
- AI can do both effectiveness and calibre analysis & can determine in real time if a machined surface needs additional machining or parameter modifications.
- Through the analysis of machine operation and component wear data, AI systems are able to forecast when maintenance is necessary for machines. Both unplanned shutdowns and maintenance expenses are avoided as a result.
- Flexibility while tackling complex tasks: AI can be used to programme a machine to operate autonomously and precisely when performing complex machining processes that are customised for different materials and workpiece shapes.
Robotic loading and unloading
The incorporation of robotic loading & unloading systems into grinding apparatus is another aspect of automation that significantly boosts output and streamlines procedures. Conveyors, robotic arms, and specialty part handling equipment are examples of these systems, which have the following advantages:
- Minimise the amount of human intervention: By automating loading and unloading processes, physical labour is not as necessary, which lowers errors and improves workplace safety.
- Continuous production is ensured and output is greatly increased by robotic systems, which can operate nonstop without becoming tired.
- Increased repeatability & precision: Robots are able to machine components with a high degree of consistency and accuracy, which is necessary for the large-scale production of high-quality goods.
Improved accuracy & quality
Nanotechnology is one of the most important developments in technology in metalworking. It is used in the production of grinding wheels. Because of their special atomic and molecular characteristics, nanomaterials can give grinding wheels remarkable wear resistance and thermal stability. These qualities have a significant effect on the accuracy and calibre of machining because they enable material to be removed from the surface to be cut in a more steady and controlled manner. After machining, the surface is noticeably smoother, which minimises or even completely removes the need for extra finishing steps. By reducing the need for extra materials, finishing time, and by increasing production efficiency, this lowers overall manufacturing costs.
In the realm of grinding apparatus, laser calibration creates new standards for unparalleled machining quality and accuracy. Modern laser calibration tools enable precise placement accuracy by enabling millimeter-by-millimeter control over the grinding disk’s location in relation to the workpiece. When grinding operations become extremely difficult and tolerances are measured in micrometres, this becomes crucial. With the capacity to measure and alter with extreme accuracy, this feature will provide a surface that is flawless and free of flaws. Because of this, manufacturers have the secret to successfully completing even the most difficult projects and satisfying the exacting standards of excellence and precision that their clients demand.
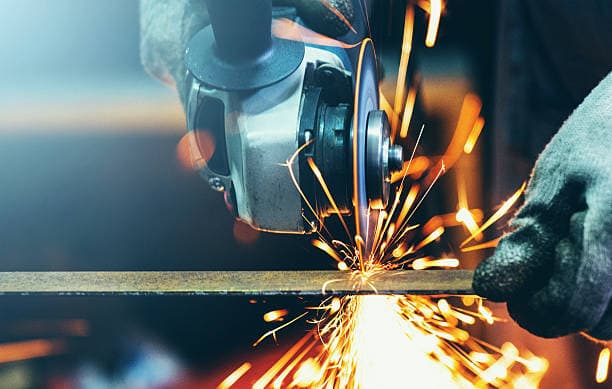
Environmental friendliness and sustainability
The companies that produce grinding apparatus are aggressively incorporating cutting-edge methods to cut down on waste & boost the energy efficiency of their equipment in an era where environmental regulations and sustainability are receiving more attention. Modern grinding machines have waste reduction systems that recycle and reuse waste in an effort to cut down on production waste. Chips that were before regarded as waste, such as grinding chips, can now be gathered and utilised as raw materials to make other products, or in certain situations, fuel. Moreover, the use of state-of-the-art abrasives and improved grinding techniques lead to optimum abrasive consumption, which in turn decreases waste by lowering the total amount of materials required. By following these procedures, the process reduces its unfavourable environmental effects, lowers production costs, and becomes more sustainable and economical.
Along with waste reduction, there has been a lot of attention paid to improving the energy-efficiency of grinding apparatus. Innovative materials and design allow for significant reductions in energy usage without giving in machine performance. Energy-saving motors, control systems that optimise energy consumption based on load, & energy recovery features enable more effective use of energy are features of new machine models. Additionally, more comfortable working environments are a major component of the companies’ social responsibility, as are enhanced insulation systems and lower noise levels. In this way, modern apparatus for grinding symbolise a sustainable production method, satisfying the efficiency & safety requirements of current environmental legislation while also promoting a safer and healthier work environment.
Structures of adaptive controls
- Individualized machining
Grinding apparatus adaptive control systems generate fresh opportunities for customised & efficient material processing. These systems’ autonomous ability to adjust in real time to shifting workpiece characteristics and process conditions leads to improved accuracy and lower failure rates.
- Real-time monitoring & correction
Using sensors and analytical tools, adaptive management systems continuously check critical factors that affectthe grinding process, such as speed, pressure, and temperature. During machining, the system can use this data to automatically adjust feed rates or pressure in order to optimise efficiency and avoid damaging the tool or item.
- Enhanced output & decreased expenses
Grinding apparatus productivity is greatly increased by adaptive management systems because of their capacity for self-tuning and optimisation. This results in shorter machining times and longer tool life, which lowers the cost of production and increases the overall profitability of industrial processes.
- Operator interaction
Adaptive methods of management offer an operator-friendly interface despite their high degree of automation. This gives workers more control over the machining process’s quality & makes it simple to modify process settings to suit the demands of a particular task.
Conclusions
Modern developments in regard to grinding technique are paving the way for revolutionary shifts in production procedures, heralding a period of never-before-seen accuracy, effectiveness, and environmental consciousness. Emerging prospects for engineering and materials processing technologies are being generated by advances in robotics, artificial intelligence, materials science, and grinding technology. We are eagerly anticipating the exciting new developments that hold the potential to completely change the business environment by raising the bar for accuracy and quality. This evolution opens the door to a more promising and fruitful upcoming period for manufacturing operations in all their facets by not only pushing the envelope of what is feasible in the sector but also emphasising the need for a more long-lasting & responsible approach to resource utilisation.