Deep within the heart of CNC milling machines lies an intricate symphony of CNC parts working in harmonious precision, giving birth to flawless components.
At the very core of a CNC milling machine resides the genius known as the CNC controller. This electronic brain processes intricate G-code instructions, orchestrating the precise movements of the cutting tool to sculpt the workpiece into perfection.
Acting as a conductor, the CNC controller interprets design specifications and translates them into exact tool movements, ensuring every cut, contour, and feature aligns flawlessly with exacting tolerances.
The Mighty Spindle
Standing tall as the powerhouse of the milling machine, the spindle holds the cutting tool with unwavering stability and imparts the rotational force that carves out intricate designs, achieving desired surface finishes with unmatched finesse. The spindle’s speed and power are crucial factors influencing the efficiency and quality of the milling process. Advanced CNC milling machines boast high-speed spindles capable of thousands of revolutions per minute, allowing for rapid material removal and impeccable surface finishes.
The Artistry of Cutting Tools
Embodying the craftsmanship of CNC milling are the cutting tools – from end mills to face mills. These tools gracefully maneuver through the workpiece, chiseling away excess material and crafting the most intricate features with surgical precision. End mills, available in various shapes and sizes, adeptly contour and profile the workpiece, while face mills excel at creating flat surfaces. Specialized tools such as ball nose cutters and chamfer mills cater to unique design requirements, providing machinists with a diverse toolkit to achieve their desired outcomes.
The Versatility of the Worktable
Forming the sturdy foundation of the milling machine, the worktable facilitates the seamless movement of the workpiece along multiple axes, unlocking limitless design possibilities and ensuring unwavering accuracy. CNC milling machines often boast rotary tables that enable continuous 360-degree rotation of the workpiece, allowing for the creation of complex cylindrical or sculpted components.
The worktable’s precision, combined with the CNC controller’s instructions, ensures every cut aligns precisely with the desired design, resulting in components of exceptional quality.
Exploring Milled Parts: Where Precision Meets Artistry
Milled parts represent the epitome of precision engineering, where form and function blend harmoniously to create flawless components of exceptional quality. Check out how CNC machine working in the video:
The Significance of Milled Parts
Milled parts reign supreme as the driving force behind diverse industries. From aerospace and automotive to electronics and medical sectors, these components play pivotal roles in enhancing performance, reliability, and efficiency. In the aerospace industry, milled parts such as turbine blades, engine components, and structural elements must meet stringent standards of precision and durability to withstand the harsh conditions of flight.
In the automotive sector, milled parts ensure the smooth operation of engines, transmissions, and suspension systems, contributing to enhanced fuel efficiency and reduced emissions. The medical field relies on milled parts to create precision instruments, implants, and prosthetics that optimize patient outcomes and improve quality of life.
The Mastery of Milling Operations
CNC milling machines wield an array of milling operations, each tailor-made to craft components of diverse shapes and complexities.
Face Milling – Sculpting Precision Surfaces
Face milling gracefully planes the surface of the workpiece, yielding flat and smooth finishes that meet the most stringent tolerances. This operation is commonly used to create flat faces, smooth large surfaces, or achieve specific surface roughness. Face milling cutters come in various designs, including high-feed face mills for rapid material removal and fly cutters for achieving mirror-like finishes.
Peripheral Milling – Carving Intricate Profiles
Peripheral milling artfully removes material from the workpiece’s edges, forming intricate profiles and contours that breathe life into complex designs. This operation is well-suited for creating slots, grooves, and complex shapes. CNC milling machines employ various cutting tools for peripheral milling, such as side milling cutters, slotting cutters, and ball nose end mills, each catering to specific design requirements.
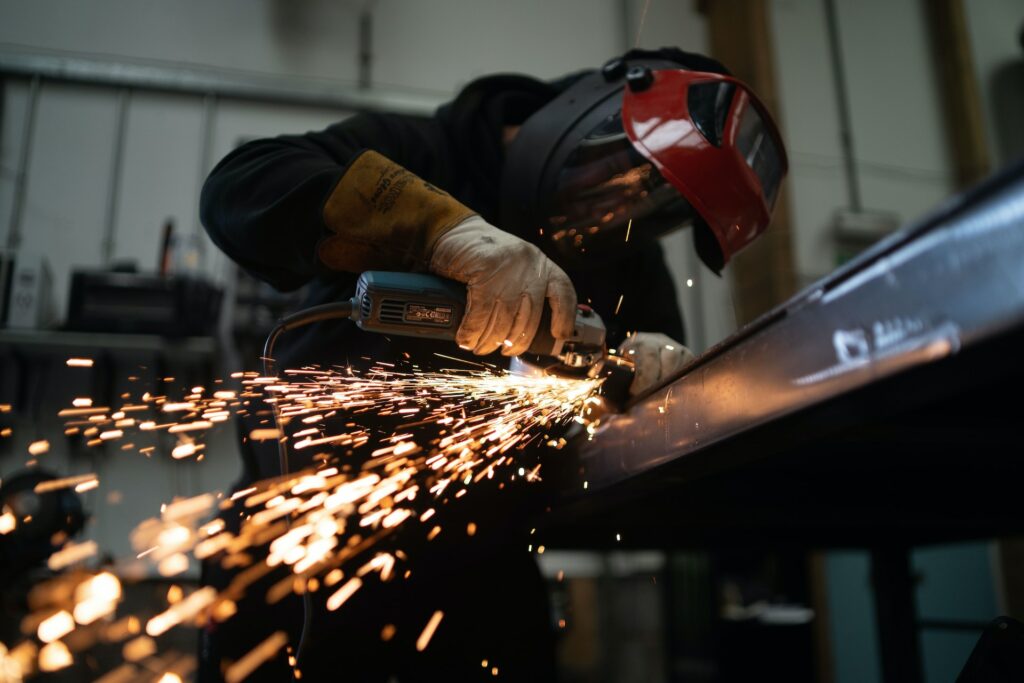
End Milling – Crafting Perpendicular Features
End milling focuses on shaping the sides of the workpiece, ideal for producing slots and features that stand perpendicular to the workpiece’s axis. This operation is commonly used to create square or rectangular pockets, keyways, and other perpendicular features. CNC milling machines utilize a range of end mills with varying flute designs to achieve precise results in end milling operations.
Drilling – Creating Precise Holes
Though not exclusively a milling operation, drilling enables CNC milling machines to craft holes of precise depths and diameters, enriching the versatility of these marvels. Drilling operations are vital in many industries, including automotive, aerospace, and electronics, where components require precise holes for assembly or functional purposes. CNC milling machines equipped with specialized drill bits deliver precise and accurate hole drilling, ensuring components fit together seamlessly.
The Magnificent Parts Crafted by CNC Milling Machines
CNC milling machines bring forth a rich tapestry of components, each an integral cog in the machinery of progress across diverse industries.
Empowering Aerospace Advancements
In the aerospace industry, CNC milling machines craft intricate components such as turbine blades, engine casings, and structural elements, ensuring peak performance and safety in the skies. Aerospace-grade materials, such as titanium and Inconel alloys, pose unique challenges, demanding CNC milling machines with exceptional rigidity and thermal stability to achieve precise results.
Driving the Automotive Evolution
The automotive sector harnesses CNC milling to manufacture engine components, transmission parts, chassis elements, and more, ushering in the era of enhanced efficiency and innovation on the roads. CNC milling machines operate tirelessly to craft critical components that endure rigorous use, ensuring the reliability and performance of modern vehicles.
Elevating Healthcare and Medical Marvels
CNC milling breathes life into medical devices, implants, and surgical instruments with unrivaled precision, ushering in a new era of healthcare excellence and patient care. Materials such as medical-grade stainless steel and biocompatible polymers demand CNC milling machines with immaculate cleanliness and precision to meet the stringent requirements of the medical field.
Pioneering Progress in Electronics and Beyond
In the electronics industry, CNC milling is instrumental in creating circuit boards, enclosures, and specialized components, underscoring the backbone of technological advancements. From microelectronics to large-scale components, CNC milling machines play a vital role in shaping the future of consumer electronics and cutting-edge technologies.
Conclusion
CNC milling parts stand as the architects of precision machining, shaping industries and propelling innovation with their artistic finesse and engineering prowess. Behind the scenes, the CNC components of milling machines work in unison, enabling the creation of flawless components that fuel progress across diverse sectors. Milled parts, with their impeccable finishes and intricate designs, continue to redefine the boundaries of modern manufacturing.
Embrace the world of CNC milling parts, where artistry meets engineering, and limitless possibilities pave the way for a future of innovation and excellence. As technology and techniques continue to evolve, the fascination with CNC milling parts will endure, inspiring generations of engineers and manufacturers to push the boundaries of craftsmanship and engineering brilliance.